Hydraulic System Failures in Fire Trucks: Prevention and Repair
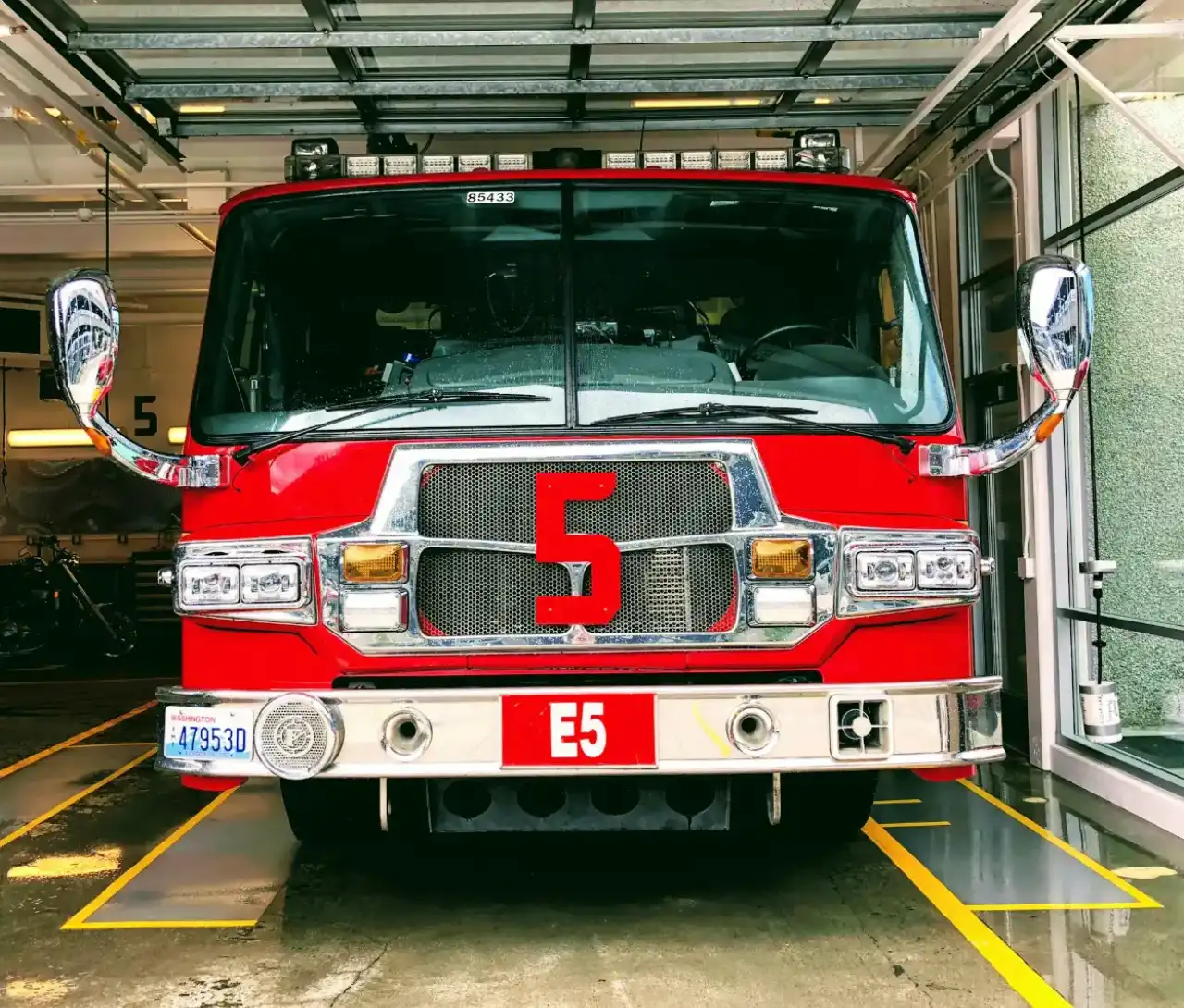
This article dives into common hydraulic system failures in fire trucks, their root causes, effective preventive strategies, and professional repair protocols.
Understanding Hydraulic Systems in Fire Trucks
Hydraulic systems are essentially high-pressure fluid circuits that convert mechanical power into movement or force. In fire trucks, they’re vital for:
- Controlling aerial ladders
- Operating rescue tools (e.g., hydraulic cutters and spreaders)
- Powering stabilizers and outriggers
- Facilitating steering and brake assists
Common Causes of Hydraulic System Failures
1. Fluid Contamination
Contaminated hydraulic fluid is one of the leading causes of premature system failure. Dirt, water, and even tiny metal shavings can clog valves, score cylinder walls, and wear out pump components.
Preventive Measure: Use only OEM-recommended hydraulic fluid and regularly sample fluid for cleanliness. Install high-efficiency filters and replace them on schedule.
2. Hose and Seal Degradation
Fire trucks operate under extreme pressure and heat. Over time, hoses can become brittle, and seals may crack or degrade, leading to leaks or complete system blowouts.
Preventive Measure: Visually inspect all hoses and fittings every 90 days. Look for bulging, cracking, or wetness—clear signs of impending failure.
3. Pump Failure
The hydraulic pump is the heart of the system. Common failure points include cavitation (caused by low fluid levels), internal scoring, and excessive heat from overuse.
Preventive Measure: Maintain fluid levels and schedule regular pressure tests. Listen for whining or groaning sounds, which often precede pump breakdowns.
4. Cylinder Wear or Drift
Hydraulic cylinders can become damaged internally, resulting in slow or erratic motion. Cylinder drift, when a component like a ladder moves unintentionally, is particularly dangerous.
Preventive Measure: Test cylinders for holding pressure during routine maintenance. Ensure proper alignment and avoid overextending components.
5. Electrical Component Failure
Modern hydraulic systems rely on solenoids, relays, and electronic sensors. Corrosion, faulty wiring, or sensor miscalibration can cause intermittent or complete system loss.
Preventive Measure: Perform electronic diagnostic sweeps quarterly. Protect wiring harnesses from water ingress and ensure proper grounding.
The Importance of Preventive Maintenance
Failure isn’t always mechanical—it’s often preventable. That’s why a structured maintenance plan is not just smart—it’s mission-critical.
BIT Inspections and Hydraulics
Under California’s Basic Inspection of Terminals (BIT) program, fire trucks must be inspected every 90 days. Hydraulic systems fall under this umbrella, making these inspections a prime opportunity to catch wear and tear before it becomes failure.
Fluid Sampling and Analysis
Just like an engine oil sample, hydraulic fluid analysis provides a window into internal component health. It can detect:
- Early-stage contamination
- Breakdown of fluid additives
- The presence of wear metals
Functional Testing
Every piece of hydraulic equipment should be run through its full range of motion during maintenance cycles. Watch for signs like hesitation, jerky movement, or unexpected drift.
Professional Repair Protocols
When failure does strike, fire truck hydraulics demand OEM-level repair. Here’s a professional workflow:
- Diagnosis: Use a hydraulic flow meter and pressure gauges to confirm the affected circuit. Diagnostic scan tools can identify electrical errors in modern control systems.
- Component Isolation: Narrow down the issue: is it the pump, a valve, a cylinder, or an electrical trigger? In some cases, temporary bypasses are used to isolate the faulty section.
- OEM or Rebuild Replacement: Never cut corners with critical components. Use OEM parts or have components professionally rebuilt to factory specs.
- System Flushing: Before reinstalling repaired components, flush the entire hydraulic circuit to remove debris. This ensures contaminants from the old failure don’t compromise new parts.
- Post-Repair Testing: Every repaired fire truck undergoes static pressure tests, operational cycle tests, and visual leak checks before being cleared for service.
Failures in California’s Heat
In San Bernardino and Rancho Cordova, temperatures regularly soar, causing hydraulic fluid temperatures to spike. Thermal breakdown of fluid is common and often invisible—until a component fails under load.
Pro Tip: In hotter climates, consider synthetic hydraulic fluid with higher thermal stability, and add auxiliary coolers to high-use circuits like aerial ladders.
Practical Advice for Fire Truck Operators
- Daily Visual Checks: Include hydraulic lines and reservoirs in your morning walkaround.
- Log Every Service: Maintain detailed records of fluid changes, inspections, and repairs for accountability.
- Train Staff: Make sure operators know how to detect abnormal sounds, movements, or smells.
Stay Ahead of Hydraulic Failures
Hydraulic failures in fire trucks are high-risk but not inevitable. Through vigilant inspections, structured BIT-compliant maintenance, and a professional repair approach, departments can keep their fleets ready for anything.
If you require fire truck repairs in California, contact Derotic Emergency Equipment today.
Contact Us
We're your one-stop shop for emergency and commercial vehicle repair and maintenance services in Rancho Cordova, Sacramento & San Bernardino, California. Get in touch with us today to schedule repairs or inquire about sales.
Locations
Rancho Cordova, CA 95742
1833 Riverview Dr, Suite E,
San Bernardino, CA 92408
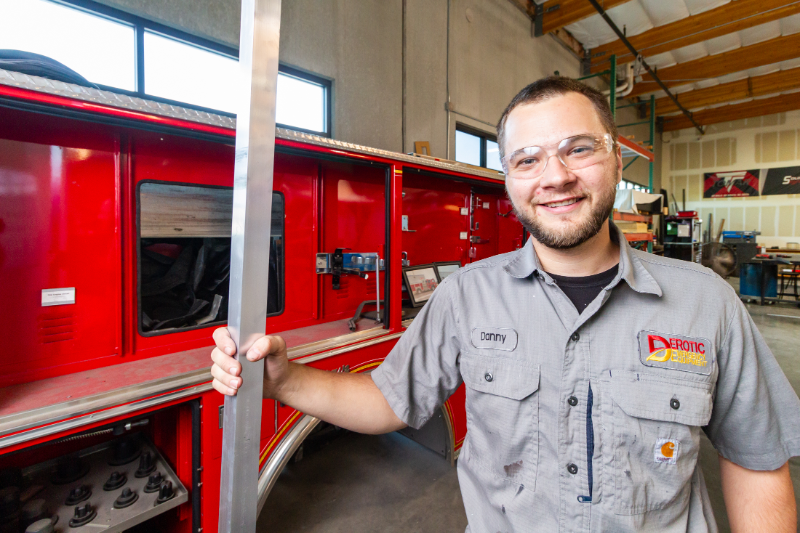